INTERN
Position 1: Process and Equipment Engineer Intern
The Process and Equipment Engineer intern will contribute to below:
• Leading critical resolution of operational needs for the Assembly/ Test process and equipment.
• Implementing the process control systems and monitoring the process to detect signals and maintain it within control, so no safety or quality incident occur and performance targets are met. Monitor equipment and process indicators to reduce process variability.
• Defining maintenance procedures, training manufacturing technicians and partnering with Manufacturing to maintain the equipment with the highest standards. Will use High Precision Maintenance methods to execute and improve preventive maintenance of the equipment. Provide basic and advance troubleshooting to manufacturing equipment including corrective and preventive maintenance.
• Coordinating, implementing and developing equipment and process improvements in regards to safety, quality and efficiency. Will use lean rules, principle and methods to determine improvement opportunities and develop solutions. Will resolve process problems by applying structured problem methodologies (Model Based Problem Solving, Lean and Statistics).
Position 2: Engineering Intern (Cost)
• Collaborate to Department Cost Representative to deliver Factory cost budget through projects and programs.
• Review, improve, and optimize processing in term of Cost idea/ equipment project that contributes to factory efficiency.
• Learn and apply LEAN/ Project management to do optimization across projects.
• Join some Working Group to assist projects that related to equipment or process.
• Drive TEGT/Factory Cost process compliance.
Position 3: Engineering Intern (Automation)
• Develop automated systems, dashboard and processes to monitor and optimize manufacturing operations
• Develop and implement robotic automation solutions to prevent quality issues. Maintain, debug errors and continue to improve those implementations
• Attending training sessions to learn the best practices from VN/ VF in automation engineering
• Monitor and analyze system performance data to identify areas for improvement
• Empowered to conduct critical data science training for TEGT operation needs.
Position 4: Engineering Intern (Quality)
• Direct observe current process across modules, analyze and find the best practice to support for compliance.
• Standardize process for tracking steps
• Build system to record the evidence, monitor and trigger if non-compliance
• Scan thru’ process and optimize process to drive for quality
• Perform experiment, analyze issue, and propose solution
Position 5: Engineering Intern (Headcount)
• Own Direct Observation to do model efficiency in department.
• Collaborate 4 shift managers/ supervisors so that we execute headcount strategy, ensure department headcount strategy is connected and executed flawlessly.
• Read factory planning and turn it to action plan of headcount planning in our department.
• Own Over-Time monitoring and coordinate to shift reps to meet ONE GOAL.
• Assist headcount project owners to complete it per task alignment.
• Hiring coordination for department.
• Work with suppliers to monitor so that supplier deliver KPIs in term of operation performance such as Attrition monitoring/ operation output, etc.
Position 6: Headcount Planning Intern (Manufacturing team)
Support to measure time run from tool/ process from manufacturing teams, manage human resource allocation for each module/ tool or production line, support with the planning on headcount and training arrangement of new hires for production. Other related tasks
Position 7: Manufacturing Integrator Intern (Manufacturing team)
• Responsible for factory loading plan and priority to meet weekly/monthly and quarterly delivery goal with the best Cycle Time
• Improve Manufacturing Delivery system
Participate in or lead working groups or task forces that support the internal factory loading plan to respond to any activities that impact the capacity.
• Escalate and follow up with other functional group if encounter any issue that potentially impact delivery.
• Drive improvement project that directly impact manufacturing operation, and delivery performance.
• To in-charge and be responsible for the smooth running of factory delivery activities. Ensure all conditions are ready to support and achieve maximum output.
• Communicate the loading plans and strategize in night and weekend shift to the factory operation team.
Position 8: Technical Training Intern
To assist in Technical Training with communications media and advertising materials to effectively represent the organization services from training services, marketing and communications to internal/external customers.
• Meets with each Technical Training discipline/group to discuss communication needs.
• Researches, writes, develop draft of marketing/communication campaigns for VNAT Technical Training that complies to Intel's branding.
• Where appropriate, arranges for the development of videos and scripts and overviews editing required.
• May develop and coordinate multimedia packages-newsletters, letters, brochures, video, bulletin board communication.
Position 9: Business Analyst Intern
• BAs perform daily, weekly, and monthly data reviews and analyses using operational metrics and reports.
• Create informative, actionable, and repeatable reporting that highlights relevant business trends and opportunities for improvement.
• He/She must have strong communication and engagement skills. In some cases, she supports SharePoint design, creating newsletter and sustaining operations indicator
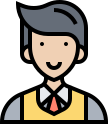
3rd/last year student with Bachelor’s degree in Electrical, Electronics, Mechanical, Mechatronics, Industrial Engineering, Industrial Management, Finance, IT, Business Administration and/or other related majors.
Additional qualifications include:
- Strong verbal and written communication skills in English
- Demonstrated excellent problem-solving skills
- Familiarity with statistical data analysis techniques
- Familiar with data analysis using programming languages such as SQL, Python, R, etc. is an advantaged
- Able to work onsite for 3-4 days per week
- Experience in semiconductor industry and manufacturing environment would be an added advantage
- Ownership mindset, detail-oriented, due diligent, good communication skill
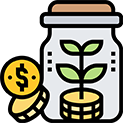
- Attractive internship allowance
- Training programs, opportunities to be involved in multinational projects
- Exciting extracurricular and sports programs for employees
- Well-invested facilities, putting safety first
- Shuttle bus system at many places in Ho Chi Minh City, Binh Duong, Dong Nai...
- High-quality cafeteria, lunch allowance, fruits, free drinks
- Safe, stable and dynamic working environment
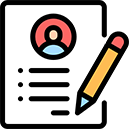
- Submit your application via the APPLY NOW button below.
- Deadline: 23:59 30/6/2023
- Note: Only selected candidates will be contacted (via email). Make sure that your email and Spam/ Promotions box are checked regularly so that you will not miss any notifications from us.